2021-05-05 16:25
由于采用轴向轧制可以使大型盘形锻件产生轴向厚度减小 、外径扩大的连续局部塑性变形 ,同时轧制时金属流动既可在圆周方向,又可在轴向, 完全符合最小阻力定律 ,所以,与大型盘形件的模锻或自由锻方法相比,该方法具有用小设备干大锻件 、节省模具费用等优点。本文以某盘件轧制生产为例 ,简要阐述了盘件的轧制工艺及其控制要点。
1 坯料的设计
盘件轧制的坯料设计必须综合考虑成形工艺的特点和要求。下面大型盘形件为例介绍坯料设计过程。
(1)根据盘件轧制的工艺要求,坯料的设计需从轧制成形原理方面进行考虑。盘件轧制过程中在上锥辊压力作用下 ,金属流动 。
(2)盘件在轧制时坯料的分配是从腹板的中心进行的。也就是说,锻件图尺寸确定后也就确定了锥辊各部位的尺寸和轧制过程中的坯料分配
(3)根据轧制轴向变形量 0~20%的要求(以轮缘处高度为基准),确定坯料的高度尺寸 。
(4)根据锥 辊模具 中心分料原理 ,使坯与锻件各部位体积分别相等。
(5)根据体积相等建立函数关系。
(6)根据 函数关系确定相应内外径的值 。 根据上述流程计算出坯料外径为1359.6 mm,内径为247.9mm。对坯料进行修正后 ,环坯尺寸为 1360amx0250mm×164mm
2 轧制工艺的优点
大型盘形锻件采用轴向轧制成形方法 ,具有如下优点 :
(1) 采用辗环机轧制技术 ,可以节约很大一部分材料。盘件材料利用率由 15%提高到 30%。
(2)用小设备干大锻件。轧制时所需最大轧制力为 5MN,远远小于模锻或自由锻所需的压力 ,即盘件轧制时只需较小的轧制力便可实现塑性变形成形 ,因而可以使锻造设备小型化 ,锻造设备的制造难度和投资也相应减小,有利于大型盘形锻件的制造和推广应用。
(3)节省模具费用。轧制时由于使用主辊、锥辊 、芯辊在较小的轧制力下使大重型盘形锻件变形成形 ,而且用同一套轧制部件便可轧制出不同尺寸的大型盘形锻件 ,从而可以节省大量的模具材料,降低模具费用。
(4)可以获得性能优良的大型盘形锻件。轧制时由于采用连续局部塑性变形的方式 ,使锻件的变形较均匀 ,可获得内部组织均匀的锻件 ,从而提高锻件的性能。
(5)可以实现大型盘形锻件的近净成形,轧制出接近零件形状和尺寸的大型盘形锻件。轧制时由于坯料的加热火次和轧制次数较少(一般1 —3次),减少了坯料的表面氧化脱皮现象 ,有利于提高大重型盘形锻件的尺寸精度 ,从而可节省大量的金属材料和机加费用 。
综上所述 ,盘件在辗环机上轧制成形 ,既提高 了材料利用率 ,又减小了后续加工余量和加工工时消耗 ,还降低了所需设备能力 ,因此具有较高的技术经济性 。
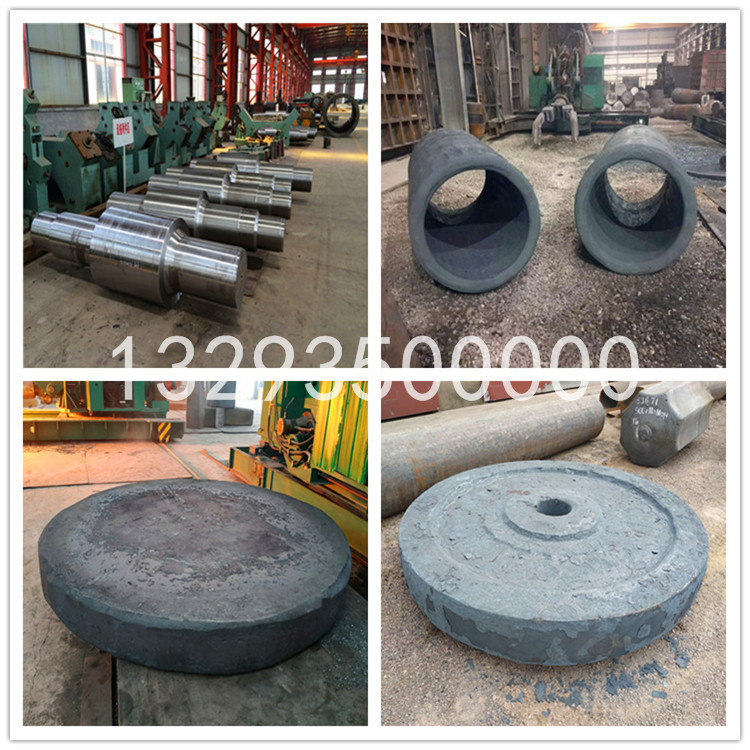
盘件轧制的坯料设计必须综合考虑成形工艺的特点和要求。下面大型盘形件为例介绍坯料设计过程。
(1)根据盘件轧制的工艺要求,坯料的设计需从轧制成形原理方面进行考虑。盘件轧制过程中在上锥辊压力作用下 ,金属流动 。
(2)盘件在轧制时坯料的分配是从腹板的中心进行的。也就是说,锻件图尺寸确定后也就确定了锥辊各部位的尺寸和轧制过程中的坯料分配
(3)根据轧制轴向变形量 0~20%的要求(以轮缘处高度为基准),确定坯料的高度尺寸 。
(4)根据锥 辊模具 中心分料原理 ,使坯与锻件各部位体积分别相等。
(5)根据体积相等建立函数关系。
(6)根据 函数关系确定相应内外径的值 。 根据上述流程计算出坯料外径为1359.6 mm,内径为247.9mm。对坯料进行修正后 ,环坯尺寸为 1360amx0250mm×164mm
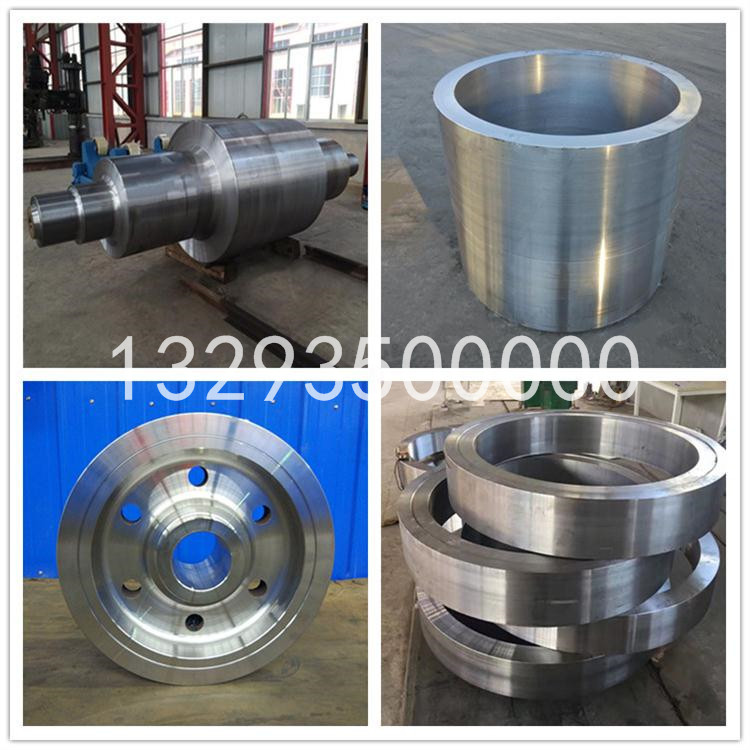
大型盘形锻件采用轴向轧制成形方法 ,具有如下优点 :
(1) 采用辗环机轧制技术 ,可以节约很大一部分材料。盘件材料利用率由 15%提高到 30%。
(2)用小设备干大锻件。轧制时所需最大轧制力为 5MN,远远小于模锻或自由锻所需的压力 ,即盘件轧制时只需较小的轧制力便可实现塑性变形成形 ,因而可以使锻造设备小型化 ,锻造设备的制造难度和投资也相应减小,有利于大型盘形锻件的制造和推广应用。
(3)节省模具费用。轧制时由于使用主辊、锥辊 、芯辊在较小的轧制力下使大重型盘形锻件变形成形 ,而且用同一套轧制部件便可轧制出不同尺寸的大型盘形锻件 ,从而可以节省大量的模具材料,降低模具费用。
(4)可以获得性能优良的大型盘形锻件。轧制时由于采用连续局部塑性变形的方式 ,使锻件的变形较均匀 ,可获得内部组织均匀的锻件 ,从而提高锻件的性能。
(5)可以实现大型盘形锻件的近净成形,轧制出接近零件形状和尺寸的大型盘形锻件。轧制时由于坯料的加热火次和轧制次数较少(一般1 —3次),减少了坯料的表面氧化脱皮现象 ,有利于提高大重型盘形锻件的尺寸精度 ,从而可节省大量的金属材料和机加费用 。
综上所述 ,盘件在辗环机上轧制成形 ,既提高 了材料利用率 ,又减小了后续加工余量和加工工时消耗 ,还降低了所需设备能力 ,因此具有较高的技术经济性 。